Natryskiwanie cieplne
Metody natryskiwania
Natryskiwanie cieplne to technologia nakładania powłok metalicznych, cermetalowych, ceramicznych i z tworzyw sztucznych na odpowiednio przygotowane podłoże elementu pokrywanego, która znalazła zastosowanie w bardzo wielu gałęziach przemysłu. Do głównych metod natryskiwania cieplnego należą: natryskiwanie płomieniowe ,natryskiwanie plazmowe, natryskiwanie łukowe oraz płomieniowe naddźwiękowe (HVOF). Źródła energii w postaci płomienia, plazmy lub łuku elektrycznego służą do nagrzania materiału powłokowego ( najczęściej w postaci proszku lub drutu ) do stanu ciekłego lub do jego nadtopienia. Następnie cząstki materiału są przyspieszane i przez strumień gazów lub sprężonego powietrza kierowane na odpowiednio przygotowaną powierzchnię. Po uderzeniu wiążą się z podłożem tworząc powłokę.
Każdy z procesów natryskiwania cieplnego ma różne koszty, możliwości materiałowe i z tym związane właściwości uzyskiwanych powłok. Technologia natryskiwania cieplnego wykorzystuje bardzo dużą grupę materiałów, jest mobilna, stosunkowo szybka i można nią uzyskiwać powłoki ochronne o grubościach od 50 – 1000 mikrometrów. Natryskiwanie cieplne to grupa różnych procesów, w których materiał metaliczny lub ceramiczny osadzany jest na powierzchnię. Głównym elementem wspólnym dla tych procesów jest to, że w każdym z nich źródło ciepła doprowadza materiał powłokowy w postaci proszku lub drutu do stanu ciekłego lub plastycznego, a potem następuje jego osadzenie na powierzchni pokrywanego detalu. Źródło ciepła jest elektryczne albo chemiczne. W zależności od materiału natryskiwanego i stosowanej metody otrzymuje się powłoki o adhezji do podłoża ~80MPa i co ważne temperatura podłoża, na które natryskiwana jest powłoka nie przekracza 200 stopni C, co oznacza, że nie zachodzi odkształcenie materiału i nie zachodzą zmiany struktury.
Rodzaje natrysku
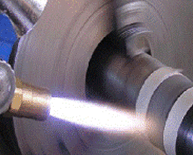
Natrysk płomieniowy proszkowy
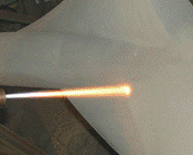
Natrysk naddźwiękowy HVDF
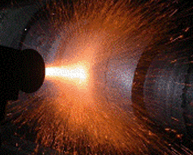
Natrysk łukowy

Natrysk łukowy

Natrysk naddźwiękowy
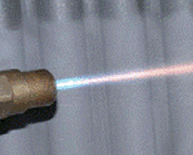
Natrysk naddźwiękowy
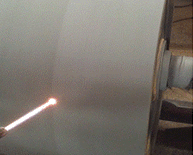
Natrysk naddźwiękowy
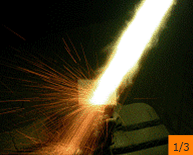
Natrysk płomieniowy proszkowy i przetapianie warstwy
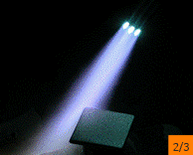
Natrysk płomieniowy proszkowy i przetapianie warstwy
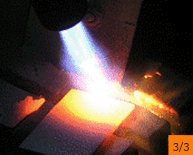
Natrysk płomieniowy proszkowy i przetapianie warstwy
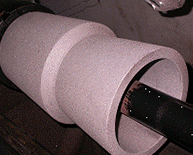
Rolka samotoku z powłoką natryskiwaną metodą łukową
Metody natryskiwania
Natryskiwanie łukowe jest jedną z metod natryskiwania cieplnego powłok, która polega na podaniu niezależnie dwóch drutów do głowicy pistoletu, gdzie generowany jest między nimi łuk elektryczny. Ciepło pochodzące z łuku topi druty. Stopiony materiał jest rozpylany za pomocą sprężonego powietrza i przyspieszany w kierunku odpowiednio przygotowanej powierzchni przedmiotu. Cząstki materiału uderzając w podłoże gwałtownie krzepną, tworząc powłokę.
Materiał: druty lite i proszkowe
Natryskiwanie naddźwiękowe jest natryskiwaniem płomieniowym. Jednak w porównaniu z konwencjonalnym natryskiwaniem płomieniowym (LVOF) w metodzie HVOF struga wychodzących z dyszy gazów ma prędkość naddźwiękową. Wysoka prędkość uzyskiwana jest przez podanie do komory spalania pistoletu natryskowego mieszaniny gazów lub paliwa ciekłego oraz tlenu gdzie następuje ich zapalenie a następnie ciągłe spalanie. Powstały w wyniku spalania gorący gaz zostaje pod wysokim ciśnieniem „wyrzucony” przez dyszę osiągając prędkość przewyższającą prędkość dźwięku (>1000m/s), pozwalającą przyspieszyć cząstki materiału powłokowego w postaci proszku do 800m/s. W innej metodzie wykorzystywana jest wysokociśnieniowa dysza – do spalania mieszanki gazów dochodzi poza nią. Do skupienia wiązki natryskiwanego materiału wykorzystuje się sprężone powietrze, które jednocześnie chłodzi dyszę. Paliwo może być gazowe (propan, acetylen, gaz ziemny itp.) lub ciekłe (nafta itp.). Proszek podawany jest osiowo sprężonym azotem do strugi gazu, lub wtryskiwany przez otwór w ścianie dyszy gdzie ciśnienie jest niższe. W wyniku tego osiąga wysoką energię kinetyczną, zostaje stopiony lub nadtopiony, a następnie osadzony na powierzchni elementu, tworząc powłokę.
Materiał: proszki metaliczne, cermetalowe
Zastosowanie
Przykłady materiałów stosowanych do natryskiwania
Chcesz nawiązać współpracę?
Skontaktuj się z nami
Wybierz sprawdzone rozwiązania
Poszukujesz partnera biznesowego, który będzie miał wiedzę i doświadczenie potrzebne do osiągnięcia Twoich celów? Nasz zespół jest gotowy do działania! Dzięki doświadczeniu w branży oraz ciągłemu poszerzaniu naszych kompetencji, jesteśmy w stanie zaproponować rozwiązania, które spełnią Twoje oczekiwania. Razem z nami osiągniesz sukces!